Inorganic Binder System
As the continuous improvement of the environmental protection requirements, the foundry industry has been seeking a 100% eco-friendly material to solve the environmental problem completely.
HA continues to pay attention to the compatibility of products and the environment, and inorganic binder systems emerges as the time require. In the European market, inorganic binder system has been widely used in engines, structural parts, new energy vehicle parts, high-speed rail parts and so on. In recent years, the demand for inorganic binder system has been growing rapidly in China, and China has become the largest market for inorganic binder application in the world.
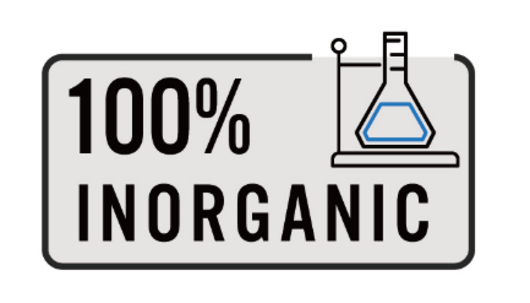
Carbon-free formulation for emssion-free casting
The principle of core production using Cordis® — HA inorganic binder system is based on type of modified silicate solution mixed with core sand and the additive Anorgit. In heated core boxes, this mixture dimensional cross-linked matrix, which gives the sand core its strength. In addition, the cores are gassed with air, heated to 130℃. The water in the cores changes into the gas phase and is expelled.
Environmental protection
- No emissions: no smoke, no BTX or BTEX, no amines, no odour nuisance
- Significantly reduced CO2 emissions
- Efficient use of resources
Productivity
- No condensate deposits on the mould means longer tool life
- High-quality castings
- Makes it possible to cast complex core geometries
- Excellent casting quality
Cost benefits
- No investment and operating costs for air purification
- No condensate formation: Reduced cleaning effort and consumption of foundry auxiliary materials
- Extended tool service life reduces costs
Improved working conditions
- No odour nuisance during the production of inorganically bound cores and during casting
- Reduced noise pollution, since no exhaust systems are required at the core shooter and casting table